1 Некоторые идут на территорию какого-то трэш-проектирования.
В современных синтезаторах повсеместно используются дисплеи и экраны, которые, обычно, сложнее интегрировать в механический дизайн, чем потенциометры и гнёзда. Производители ещё как-то пытаются решать такие задачи для готовых устройств, в то время как самоделкины обычно просто забивают1 на стёкла и в передней панели остаётся зияющая дыра с неприкрытым дисплеем под ней.
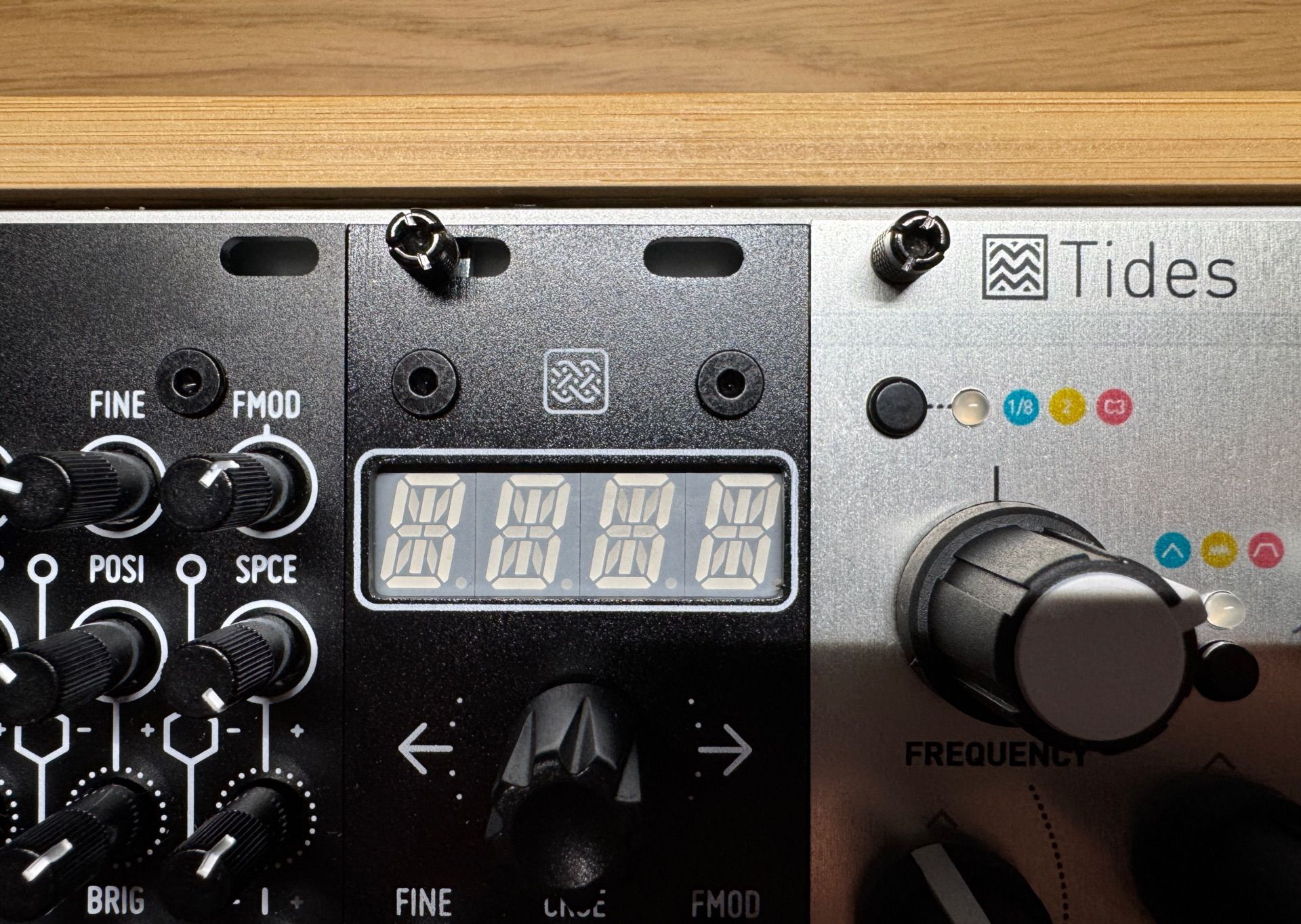
Расскажу о простейшем способе сделать «стекляшку» на экран вашего девайса. Чтобы все кругом говорили «Где ты такое купил?! Мне такое тоже нннада!». Способ подходит для любой электроники в которой есть некрупный дисплей и плоская передняя панель.
Для того чтобы сделать стекляшку не используя сложные рамки-безели, прокладки, светомаскировку и другие взрослые технологии, достаточно из куска прозрачного пластика вырезать её на 1-2 мм больше окна в которое она будет установлена и на эту разницу сделать «ступеньку». Ничего не понятно, поэтому у меня есть картинка.
Такое стекло будет защищать дисплей от пыли, пальцев и всего остального, что ему может повредить. При этом у стекла будет общая поверхность с лицевой панелью и устройство будет выглядеть совсем по-другому.
Глубокая гравировка
2 Как закрепить заготовку, где начать и закончить, сколько проходов сделать, какую фрезу использовать и пр.
В сферической ситуации в вакууме, лучший способ сделать ступеньку на пластике — небольшой фрезерный станок. Но в реальной реальности, где вам нужно сделать всего пару таких стекляшек, фреза потребует неоправданно много подготовительных работ. Нужно будет придумать стратегию обработки2 и разобраться с CAM-процессором чтобы сгенерировать программу под имеющиеся расходники. Но главное препятствие: фрезерные станки не так распространены, как CO2-лазеры. Не верите — поищите на картах компании, которые занимаются лазерной резкой и сравните с количеством тех, которые фрезеруют.
Поэтому мы уберём эту ступеньку при помощи глубокой гравировки используя обычный лазер из соседней подворотни. «Глубокая гравировка» — ключевое слово. Можете погуглить его на любом языке и найдёте множество описаний этой, с позволения сказать, технологии.
Материалы
В качестве материала в первую очередь вспоминается поликарбонат, как один из самых прочных из доступных листовых пластиков. Но он горит под CO2 лазером, а его прочность не даёт преимуществ на таких малых поверхностях. Вместо него я использовал акрил, известный в народе как «оргстекло».
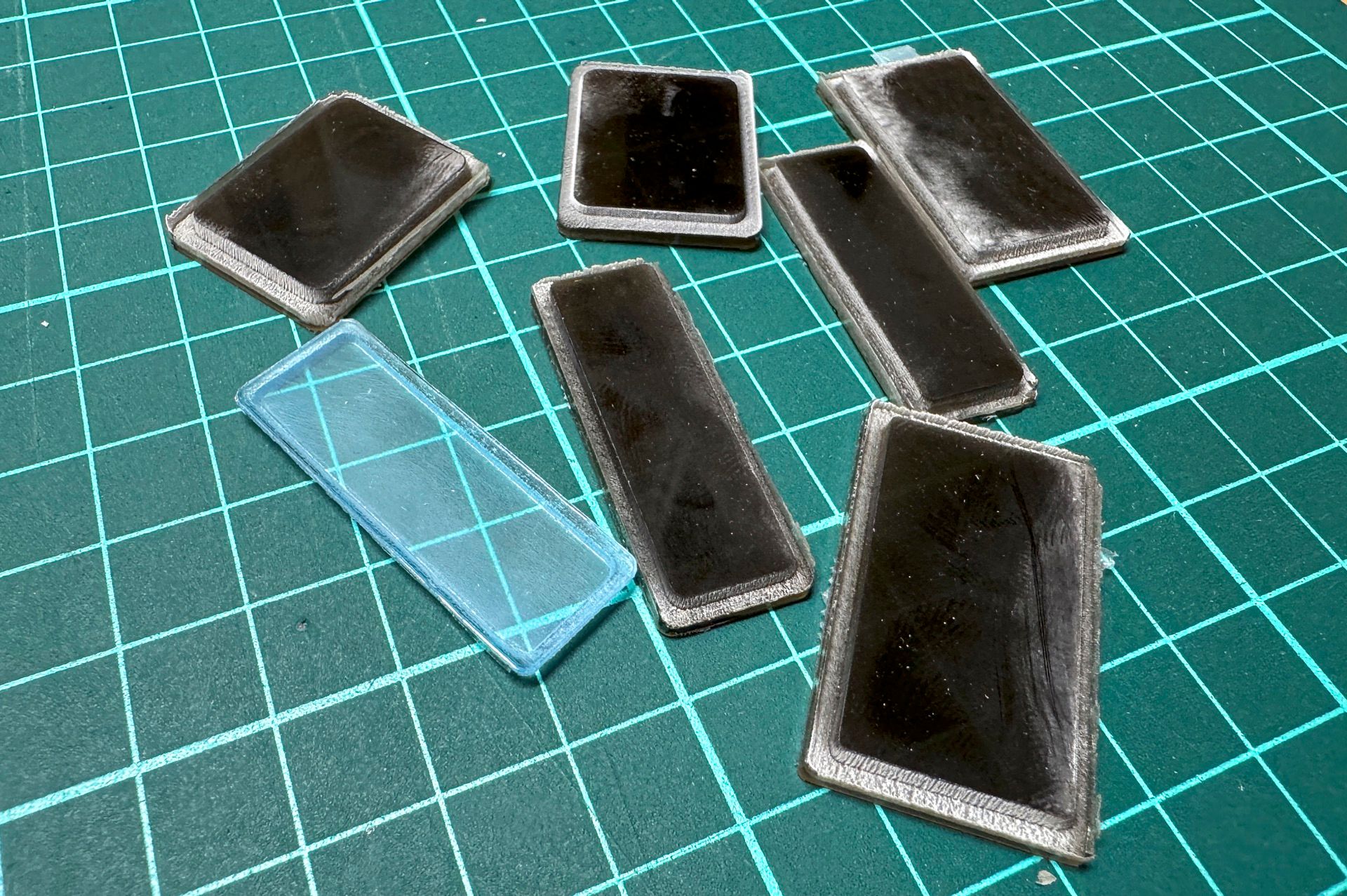
У акрила низкая твёрдость и он легко собирает мелкие царапины на поверхность, но мне не кажется это каким-то значительным недостатком, когда мы говорим про самодельную электронику. Если вам это важно, можно сделать несколько стекляшек враз — они вообще не стоят денег.
Акрил бывает экструдированный и литой. Экструдированный лучше подходит для резки потому что даёт кристально чистый срез. Литой лучше подходит для гравировки потому, что даёт снежно-белую, контрастную поверхность. Для наших задач приблизительно пофиг какой именно акрил оказался у вас под рукой.
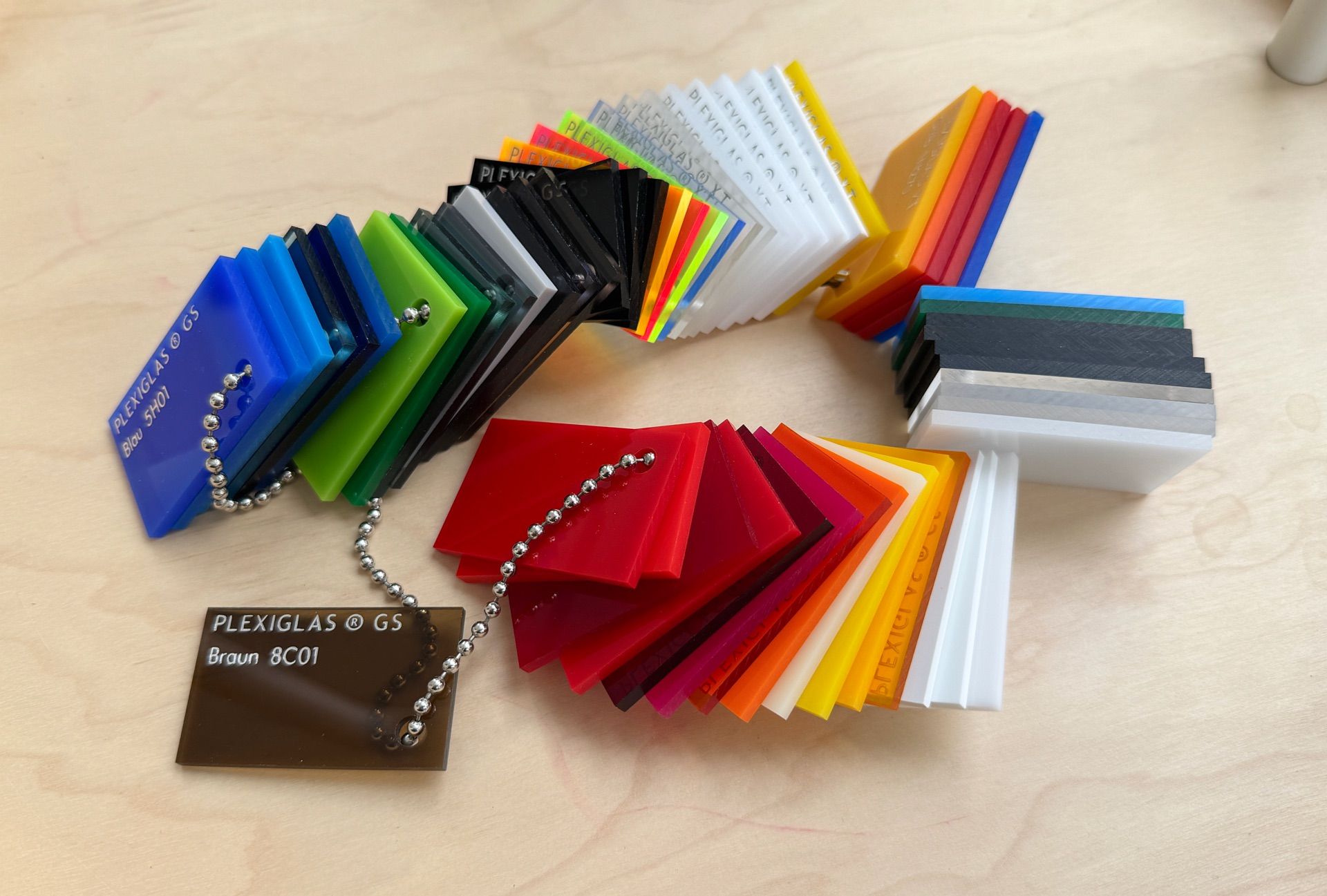
Последняя важная характеристика — цвет. Можно использовать полностью прозрачный акрил, а можно полу-прозрачный цветной. Во втором случае имейте ввиду, что цвет будет не только маскировать, но и фильтровать свет от вашего экрана. Это одновременно плюс и минус. Когда я, 2 года назад, делал свою первую стекляшку, то выбрал красивый пластик рубинового цвета для установки на зелёный 14-сегментный дисплей. Он, безусловно, роскошно выглядел в выключенном состоянии, но когда я включал модуль, дисплей очень тускло светил оранжевым потому, что весь зелёный компонент из него был отфильтрован.
Я использую литой акрил бренда Plexiglass GS в цвете Braun 8C01 толщиной 3 мм.
Толщина лицевых панелей синтезаторов обычно 2 мм — тот объём материала, который нужно снять глубокой гравировкой. Оставшийся 1 мм сформирует ступеньку, которая не даёт стеклу вывалиться наружу и за которую, при необходимости, его можно приклеить изнутри.
Макет
Тут вообще нет ничего интересного. Тонким чёрным черчу в векторном редакторе внешний контур по которому будет проходить резка, а область гравировки целиком заливаю любым другим цветом. Если у вас нет векторного исходника панели, то можно отсканировать её, или даже просто сфоткать и подложить под чертёж фоном. Скопировать соотношения сторон и радиусы скруглений и потом масштабировать в реальный размер.
Макет выглядит примерно так. По чёрному режем, красный — гравируем.
Экспортирую два отдельных файла: в одном информация только для резки, во втором — только для гравировки. Это нужно чтобы иметь возможность быстро применить разные настройки лазера и не копаться в автоматизации.
Настройки лазера
Кажется нет большого смысла в описании конкретных настроек из-за того, что лазеры у всех разные. Я использовал станок Epilog Fusion M2 с трубкой на 35 Вт. Расскажу об общих принципах и выводах к которым пришёл опытным путём.
Основные параметры: скорость и мощность, для глубокой гравировки сильно отличались от рекомендуемых. Фактически я гравировал на полной мощности, а скорость движения сильно занижал. Драйвер просит указать DPI для гравировки и я выбрал 600 точек, но напоминаю, что макет целиком был векторный.
Параметр, который сильнее всего повлиял на результат, и увеличил скорость и качество глубокой гравировки — это Dithering — алгоритм по которому лазер считает движение на цветовых градиентах. В драйверах моего лазера было 5-7 разных алгоритмов, но лучше всех показал себя Stucki.
В итоге 2 мм акрила получается снять всего за 5 проходов, которые можно выполнить без перефокусировки лазера.
На первых подходах мне показалось, что высоту стола нужно менять, после каждого прохода гравировки, чтобы фокус лазера оставался на нужном месте. В итоге в документации на станок вычитал, что точная фокусировка не так важна. А что действительно важно, так это хорошая вытяжка. При гравировке акрил будет выделять много вонючей дряни, значительная часть которой будет оседать прямо на стекле, но в итоге легко смоется любой жидкостью в которой есть спирт.
Дефекты и доработки
Получаются довольно аккуратные детали. Есть некоторые особенности, большинство из которых, уверен, связаны с конкретным станком, а не с самим процессом. Например, на внешнем контуре ступеньки остаётся тонкая «наплавка». Я не знаю причины её образования, но она легко удаляется ножом, напильником, или даже пальцем.
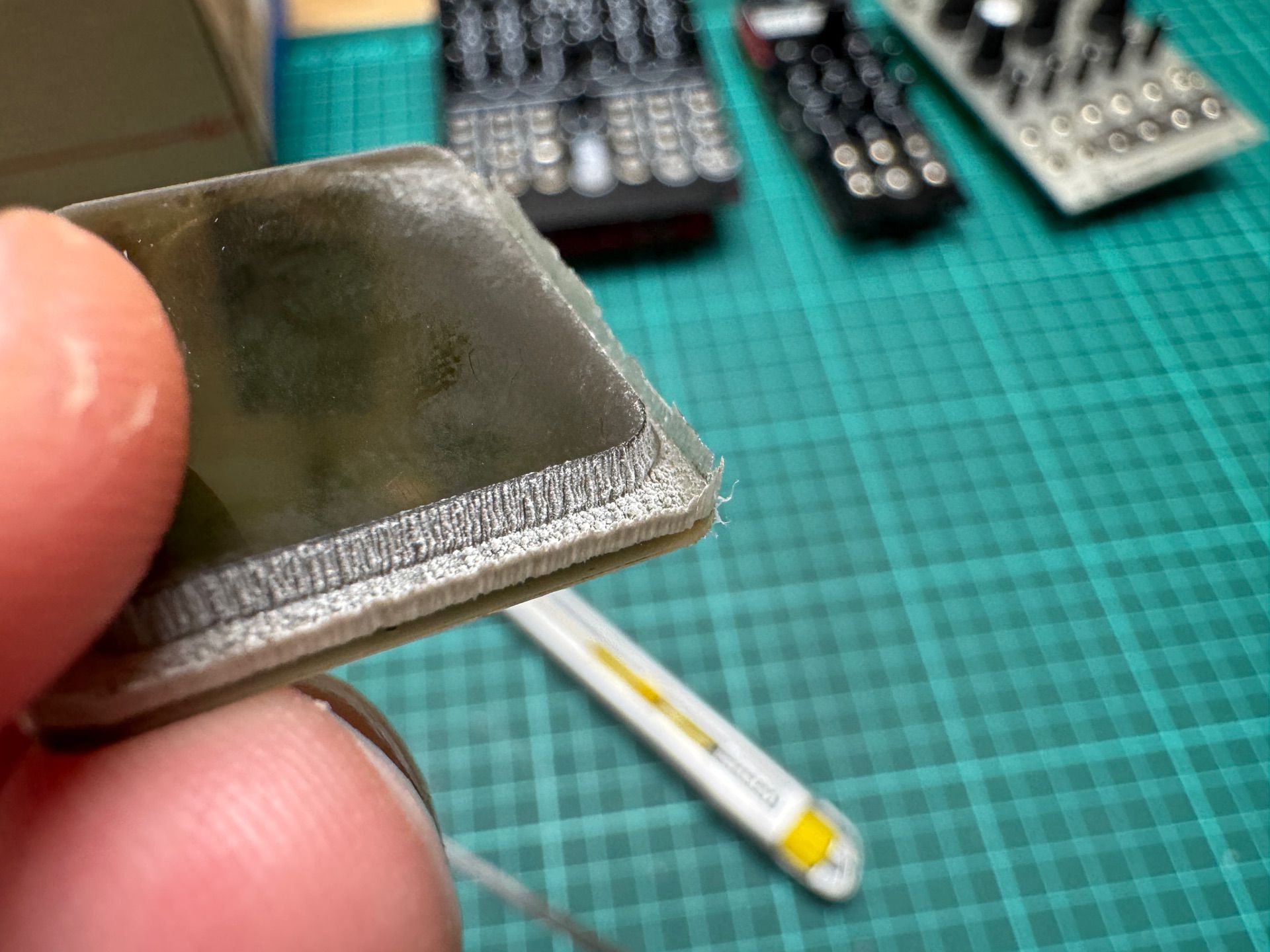
Или другой дефект: часть ступеньки которая находится ближе к точке старта, не плоская. Это тоже ни на что не влияет и источник проблемы мне неизвестен. Думаю оба этих дефекта можно исправить если в конце выполнить какой-то «чистовой» проход на малой мощности и высокой скорости.
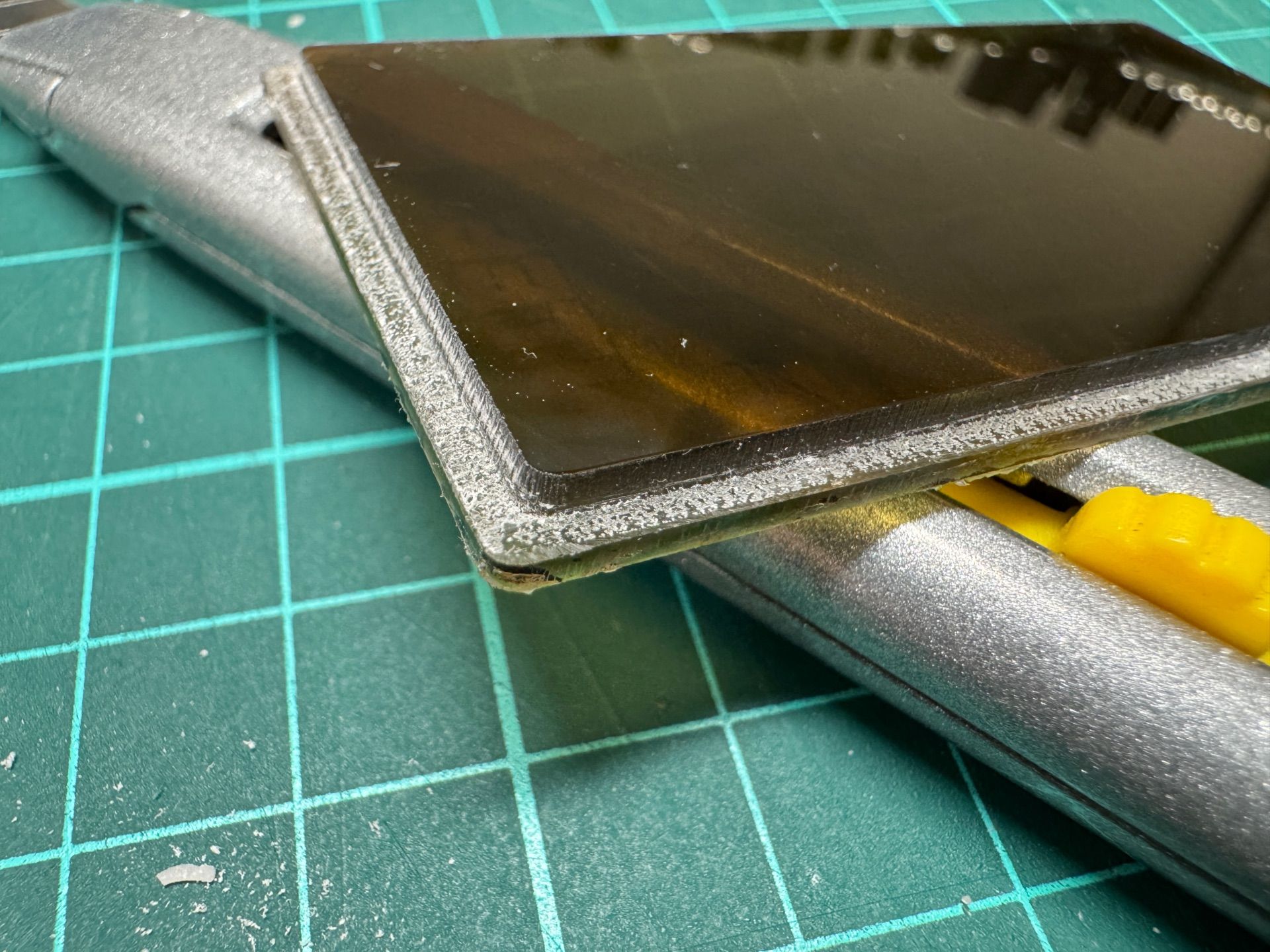
И ещё: я сначала выполняю резку, а потом гравировку, но, возможно, правильнее делать наоборот. При этом можно настроить мощность лазера при резке так, чтобы луч резал на глубину 2 мм. Не насквозь. С этими настройками можно проехать по внутреннему контуру и тогда его грани станут идеально вертикальными. Но на деле всё это не важно до тех пор, пока вы не гравируете эти стекляшки пачками.
Как клеить
Никак. Из 5 стёкол, что я сделал недавно, я не приклеил ни одно. Механика всех устройств была на столько плотной, что зазора между лицевой панелью и дисплеем хватало как раз чтобы это стекло установить. Оно не болтается и не может вывалиться ни наружу, ни внутрь.
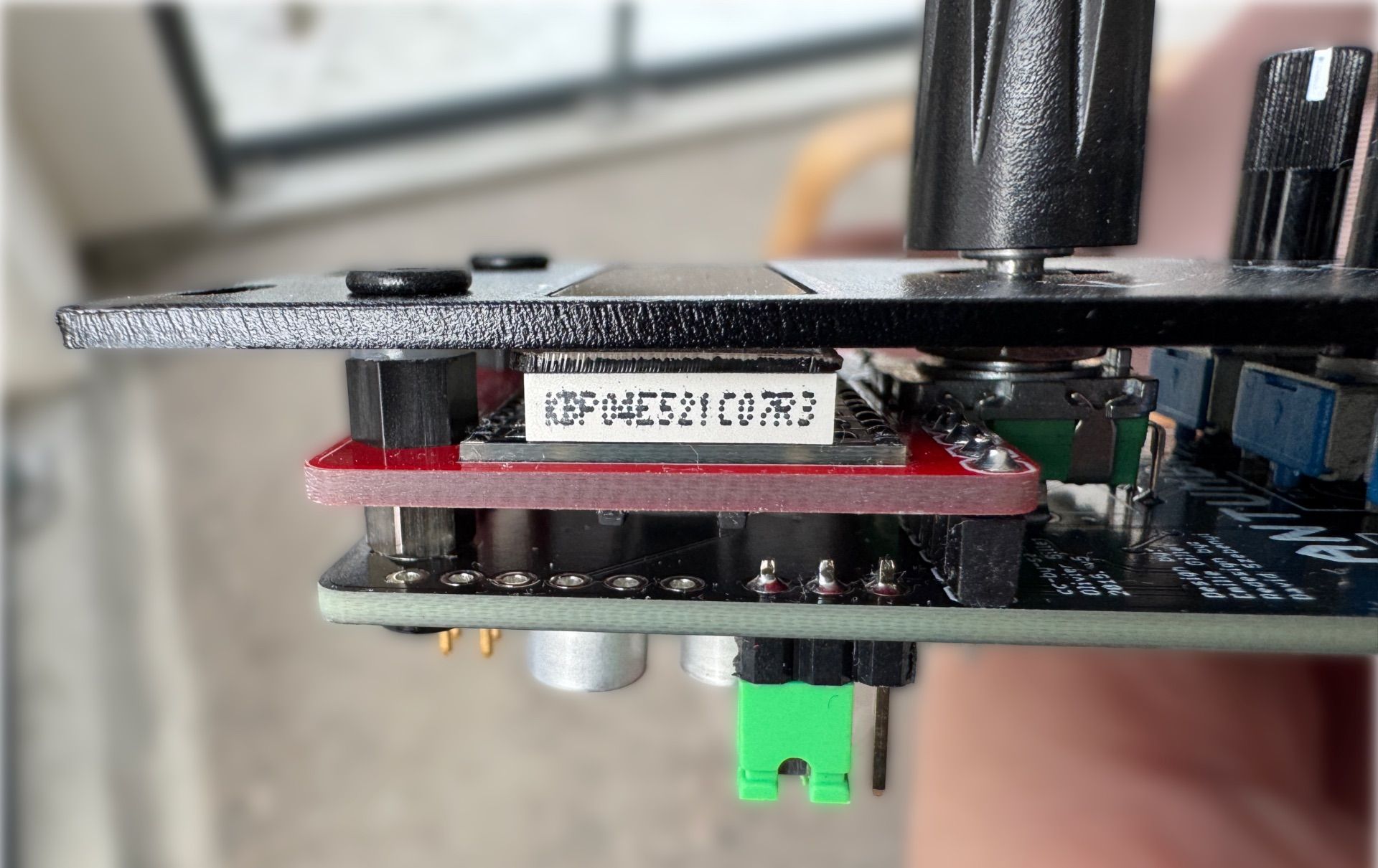
Если всё же хочется надёжно приклеить стекляшку, то я рекомендую использовать клей, который, после отвердевания, сохраняет хотя бы минимальную пластичность. Вот Томми Килландер вообще рекомендует использовать обычный ПВА вместо того, чтобы изобретать велосипед.
Клей, который я точно не рекомендую — цианакрилатный. Суперклей, Космофен — вот эта семейка. Мало того, что нужно иметь нечеловеческую аккуратность при работе с такими текучими адгезивами, так они во время высыхания ещё эмитируют свои компоненты в атмосферу оставляя на поверхностях отчётливый белый налёт, который почти невозможно удалить.
В то время, как цифровые синтезаторы в округе плохо звучат, ваши — плохо звучат и блистают.
⚠️ Каменты в режиме эксперимента. Нужна регистрация на GitHub и необходимо дать разрешение боту Giscus. Если это неприемлемо, можно комментировать прямо на GitHub.